Revolutionize manufacturing with advanced injection molding
Experience the Future of Manufacturing with our Cutting-Edge Injection Molding Technology
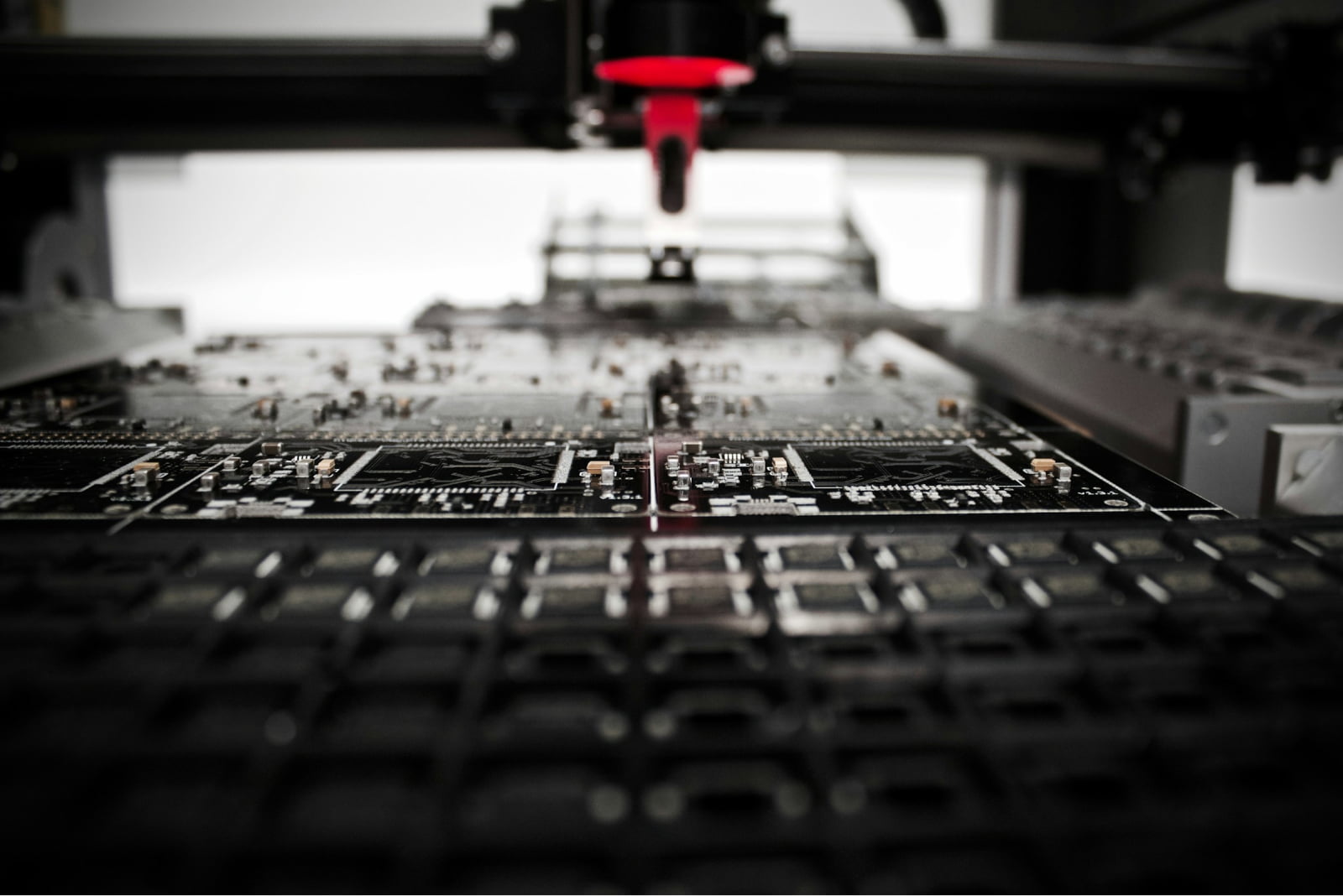
Advancing Injection Molding Technology for Complex Products
MULTI- FUNCTIONAL-N-MOLD-ELETRONICS
Discover how the MULTIMOLD project redefines the landscape of injection molding technology, enabling the production of complex products with improved haptic interfaces, embedded electronics, and sustainable manufacturing practices.
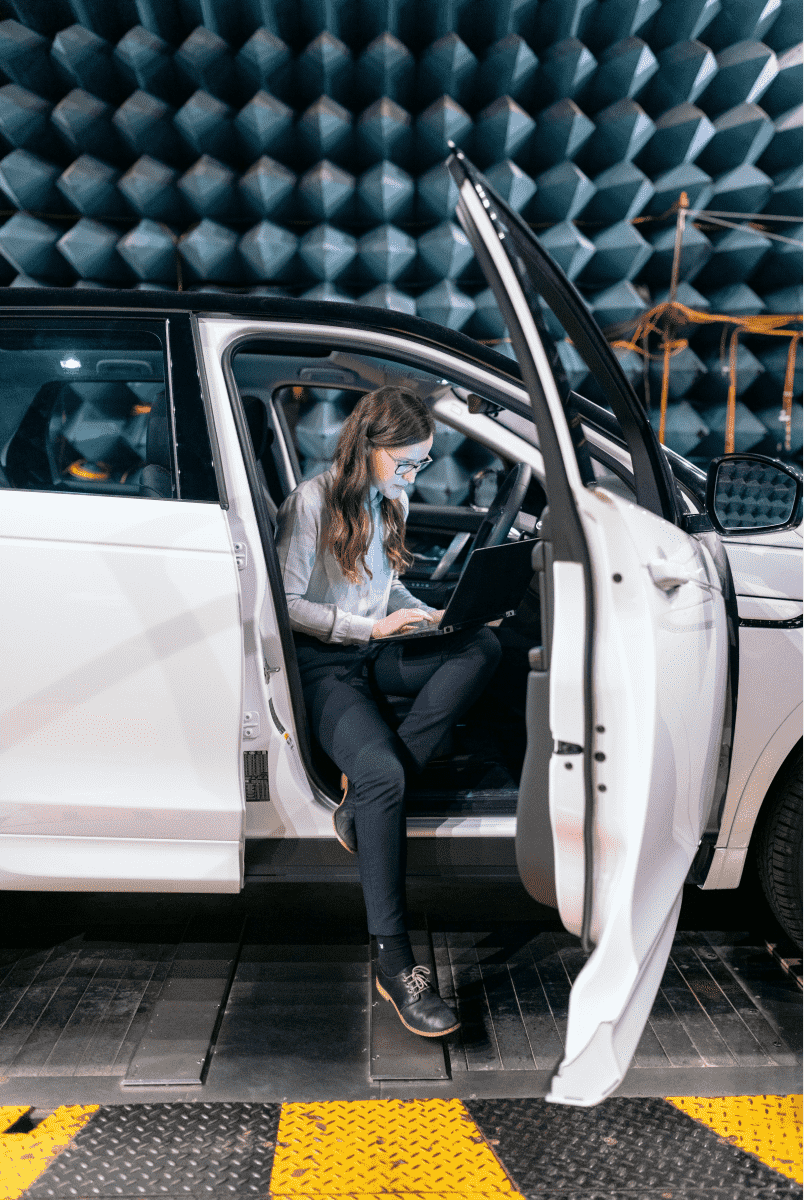
Discover the Future of Manufacturing
Unlock the potential of injection molding technology for your business.
Discover how MULTIMOLD leverages the potentiality and revenues of inject molding
MULTIMOLD innovative approach provide a solution for manufacturing sector to face the challenges of in-mold electronic (IME) processes for complex and high - precision products with embedded electronics, optics, and advanced surface functionalities
Improved user experience and surface functionalities
MULTIMOLD will enhance users experience even in challenges conditions like wet and dirty environment thanks to high-tech solutions to improve surface functionalities.
Sustainability
MULTIMOLD prioritize sustainability by focusing on recycling and reducing environmental impact throughout the manufacturing process.
Boosting efficiency and revenues
MULTIMOLD employs digital models, data management, and machine learning to enhance control over the fabrication process, ultimately improving efficiency and yield.
Circular - by - Design
MULTIMOLD offers a solution that is Circular - by- design. We build the product to separate easily electronics components from the plastic and allow reusing and recycling of materials.
Discover the Future of Manufacturing
Unlock the potential of injection molding technology for your business.
Use cases
Discover how the MULTIMOLD project is advancing injection molding technology to manufacture complex products with some real use cases from pivotal manufacturing sectors.
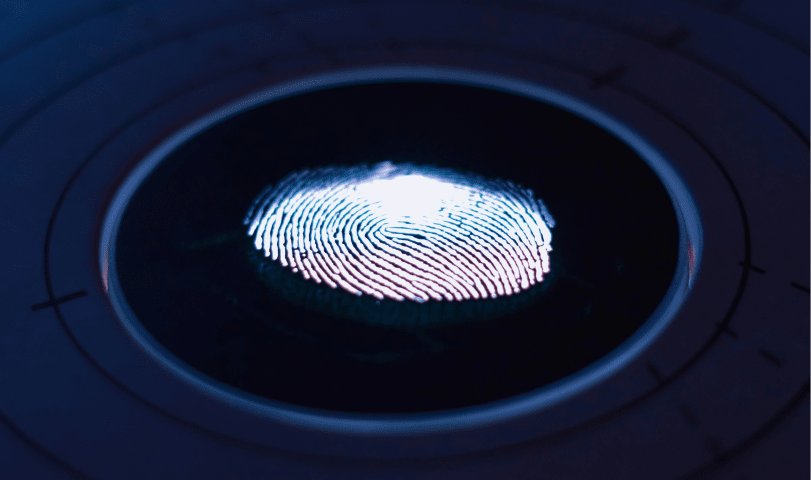
Automotive Sector:Human Machine Interface for car exteriors
MULTIMOLD solutions offers a customizable product design that integrates touch functionalities for car exteriors, even in conditions prone to wetness, dirt, and glove usage.
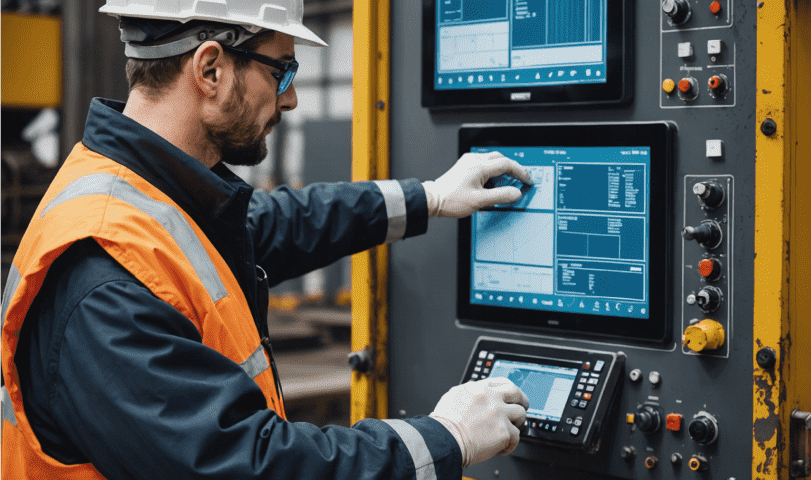
Industrial Sector: Industrial Operator Interfaces
The MULTIMOLD process will allow the adoption of Industrial Operator Interfaces for Industrial control panels that require reliable, well-perceivable haptic responses to the user interaction usually in harsh environmental conditions
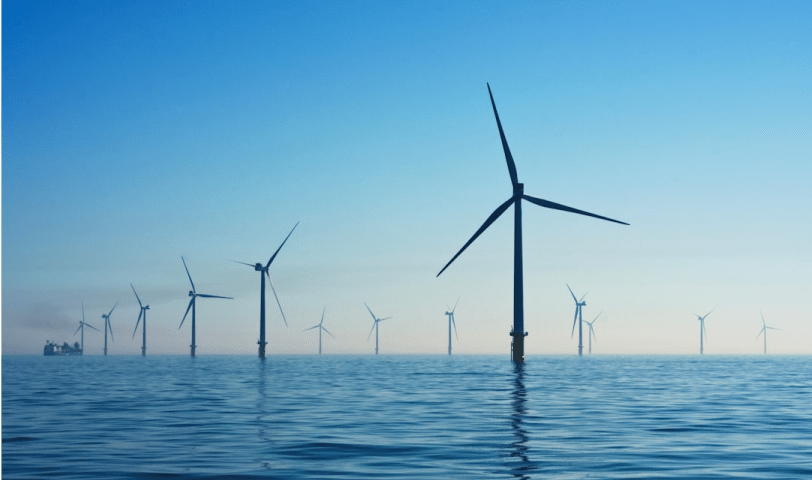
Wind Turbines: Overmolded electronics in condition monitoring (CM)
The MULTIMOLD condition monitoring electronics are applied in the rotor blades of a wind turbine to reduce costs by embedding complex and sensitive electronics in plastic and with the use of a fast injection molding process.
Discover the Future of Manufacturing
Unlock the potential of injection molding technology for your business.
Meet Our Team
Get to know the experts behind MULTIMOLD.
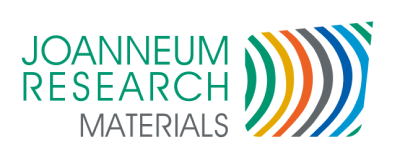
JOANNEUM RESEARCH, headquartered in Graz, is a successful national and internationally active research institution owned by the Austrian federal states of Styria, Carinthia and Burgenland. JOANNEUM RESEARCH MATERIALS is the Institute for Sensors, Photonics and Manufacturing Technologies. MATERIALS provides access to the latest technologies required for implementing innovative products and services.
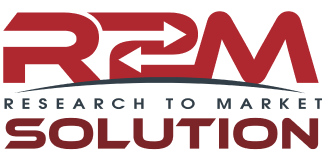
R2M Solution fills the gap between research activities and market implementation. Expertise in Innovation, Engineering, Sustainability, Energy and ICT.

imec-cmst is an imec associated research lab at Ghent university. Our research is focused on smart microsystems integration and design. We work in 3 application domains: Smart Objects for IOT, Flexible Microsystems for Health and Optimal Microsystems.
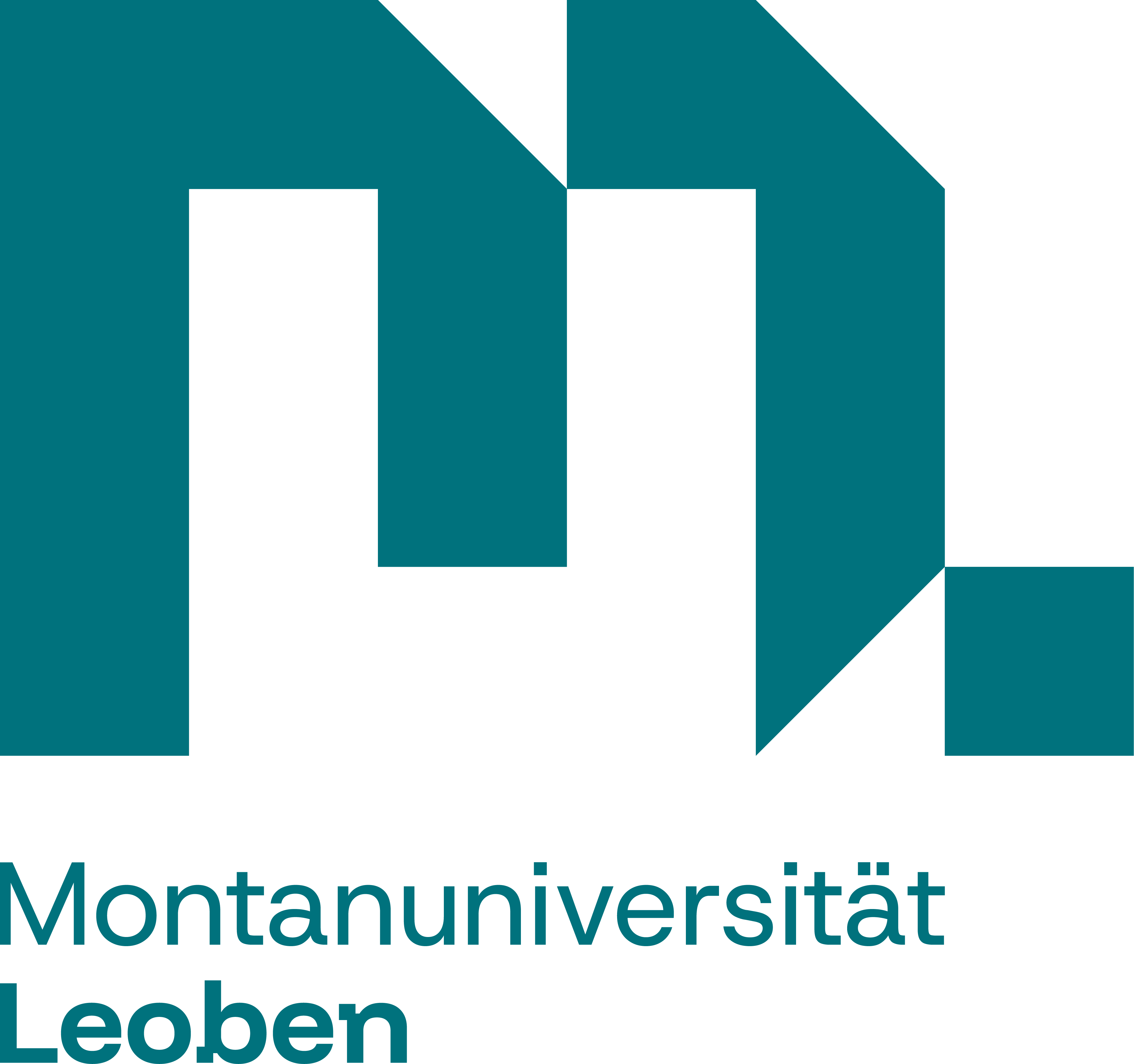
Montanuniversitaet Leoben (MUL) is a technical university dedicated to unique core disciplines aiming at establishing sustainability in its value-added cycle, that starts from the production and processing of raw materials to finished products made of high-performance materials, on to the disposal of the products and their recycling and reuse as secondary raw materials. In this project the Institute of Polymer Processing of the Department of Polymer Engineering and Science is involved.
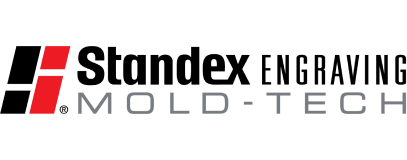
At Standex Engraving Mold-Tech, we optimize Surface Performance by creating textures on the tooling that manufactures products we all use every day. We are one global company in 37 locations, with the same approach to taking care of our customers. We make it easy by offering a full range of services: Laser and Chemical Engraving; Nickel Tooling; Architexture Design Studio; Tool Enhancement and Tool Finishing.
Trust the premier, global supplier for mold texturing and surface finishes to add creative beauty and function to your product. Standex Engraving Mold-Tech is one of five segments of Standex International Corporation (NYSE: SXI).
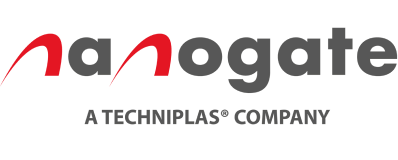
Nanogate is a highly experienced company at IML- business. Outgoing from producing decorative IML- foils Nanogate hast started with printed electronics in 2019 and has established a wholf IME inhouse process chain. The main business fields are the production of serial IML- foils for automotive and non- automotive industry, but also process engineering, prototyping and preseries of printed electronics, IME and IML-parts.
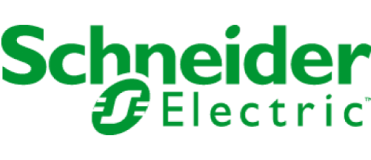
Schneider Electric is a French multinational company that specializes in digital automation and energy management. It addresses homes, buildings, data centers, infrastructure and industries, by combining energy technologies, real-time automation, software, and services. It operates with more than 128000 employees in over than 100 countries.The Control & Signaling activity is part of the Industrial Automation Business Units of Schneider Electric. Its 150 employees are creating and managing products offers covering operator interfaces (pushbuttons, stack lights) and machine control (relays). Schneider is the worldwide leader in operator interfaces.
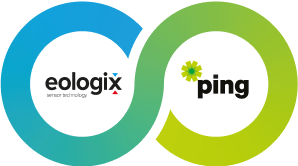
At eologix-ping, we dedicate ourselves to optimizing wind turbine performance. Our tailored advanced sensor systems detect issues like icing, blade damage, and lightning strikes, providing crucial data for informed decisions. Our solutions seamlessly integrate, ensuring peace of mind and maximizing turbine efficiency.
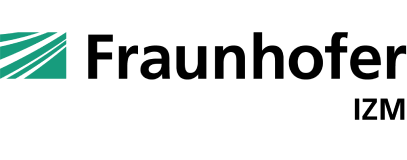
Fraunhofer IZM is a world-leading research institute for microelectronics and systems integration. The unique engineering profile is complemented by the activities of the Dept. Environmental and Reliability Engineering on “Green Electronics” right since the establishment of the institute in 1993. With more than 350 researchers, Fraunhofer IZM represents a unique combination of technology development and related environmental expertise.
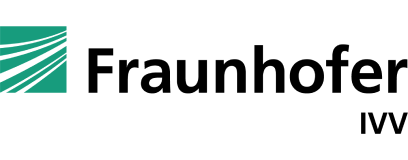
The Fraunhofer Institute for Process Engineering and Packaging IVV will participate in this project with a focus on the recyclability of the developed test vehicles. In general, the department ‘Process Development of Polymer Recycling’ of Fraunhofer IVV deals with the separation of pure polymers from plastic containing waste by means of mechanical pre-treatment and physical dissolution.
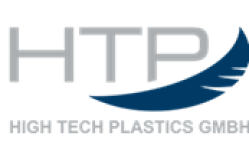
HTP will play a pivotal role by leveraging its decades of experience and technological expertise to develop and implement hybrid solutions that meet the demands of Industry 4.0 and digitalization. Focusing on electric mobility, sustainable solar energy, and advanced robotics, HTP will integrate smart surfaces into plastic components and assemblies, ensuring the highest standards in quality, delivery performance, service, technical competence, and operational readiness. Our innovative approaches, including multi-component injection molding and advanced painting techniques, will drive the success of next-generation products.
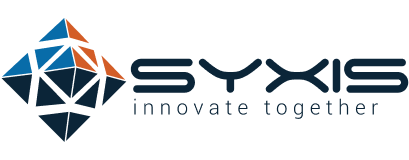
Syxis is a Digital Sustainable company that connects SMEs, organizations, and research centers across Europe to generate and foster innovation. Syxis establishes and facilitates new relationships among companies operating in the field of funded research and innovation, assisting them with methods, operations, and technologies. This enables them to embrace and develop new strategies focused on themes such as digitalization, circular economy, and networking.
News
Read what industry experts and partners have to say.
Discover the Future of Manufacturing
Unlock the potential of injection molding technology for your business.
Contact us
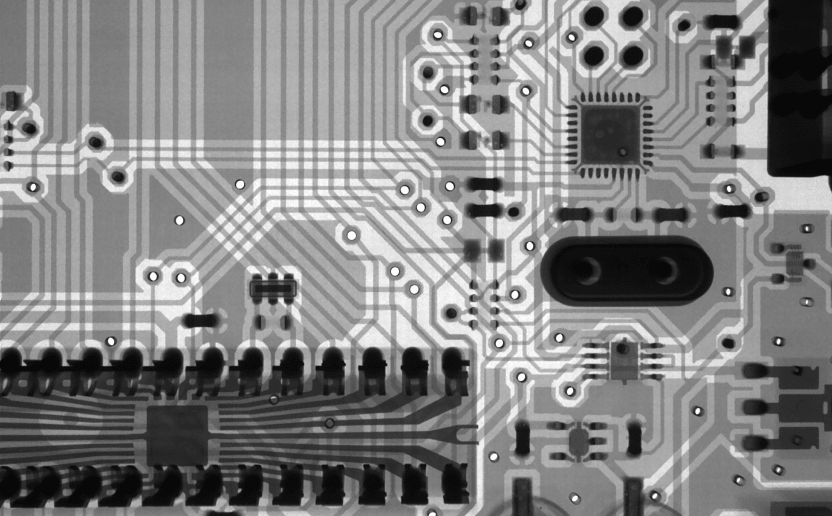